
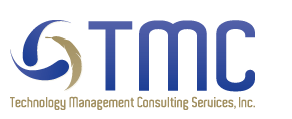
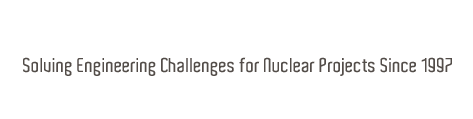
Case Studies
Establishment of Manufacturing Capability
Primary Engineering Discipline: Nuclear Engineering
Client: Los Alamos National Laboratory
This project was undertaken to establish the ability to manufacture components at Los Alamos National Laboratory (LANL). The manufacturing facility was a combination of existing equipment and equipment transferred from a decommissioned facility. Much of the design basis of the equipment was unavailable. Some of the manufacturing processes were different from those for which the equipment was originally designed and used. The manufacturing organization, procedures, and support structure were developed as the equipment was being installed. The concept for the program was to qualify the manufacturing process in parallel with the development of the equipment and manufacturing support infrastructure.
TMC’s task was to develop and implement Process Qualification Plans (PQPs) to establish the operational bases that would otherwise have flowed down from the design, construction and startup testing life-cycle phases.
LANL staff used procedures and guidance provided by TMC to perform initial screening of manufacturing processes and then selected processes with significance relative to the design requirements. TMC then prepared Process Qualification Plans (PQPs) for the essential production processes.
The PQPs developed by TMC identified tests and experiments that, when implemented, would demonstrate that the tools, equipment, materials, process steps and constraints would result in products that met design requirements. These tests were conducted in parallel with the development of the production support infrastructure, such as the change control, calibration, software quality assurance, training, and production control programs. When integrated together, the PQPs, test results and associated working procedures addressed the production facility acquisition and life cycle needs from the design, construction and startup phases and resulted in a set of information supporting the initial stages of the production life-cycle phase.
Deliverables were approved manufacturing systems and working procedures that were integrated into the manufacturing system infrastructure and which allowed initial manufacture of products that could be certified by the product design agency. These procedures were integrated with the supporting facility and its safety requirements as recorded in process hazard control plans.
A distinguished performance award was received by TMC for its work on this project
Glovebox Criticality Analysis
Primary Engineering Discipline: Nuclear Engineering
Client: Johnson Controls of Northern New Mexico
The Glovebox Criticality Analysis project was an evaluation of several test configurations to ensure criticality safety for a glovebox storage area at Los Alamos National Laboratory.
These fissile parts were accumulated or staged in the fabrication area before being transferred to the next step in the manufacturing process. A parts-staging glovebox system was required to conduct specific inventory activities and to hold the parts in various geometries. The glovebox system segregated the components from other parts and other materials, protected the components from exposure to air and minimized the exposure of production personnel to the parts. Because the glovebox system was to be used to store fissile material, it was necessary to ensure that a criticality event cannot occur under any conditions. The primary method of preventing criticality was to control the system dimensions and the number of parts in storage, although administrative controls were also to be employed.
For this project, TMC performed criticality safety evaluation as part of a safety engineering effort. To perform the criticality evaluation of the proposed glovebox tests, TMC provided an expert in Nuclear Engineering with over 35 years of experience in the field. This experience included performing nuclear criticality safety analyses for manufacturing, shipping and storing fresh fuel for power reactors and test reactors and for spent fuel shipping and storage, including light-water reactor spent-fuel storage.
As a starting point for the safety engineering evaluations, TMC analyzed several glovebox storage test configurations for criticality using three separate hand-calculation methods. For each array, unit mass loading, and fissile type, the hand calculations determined the minimum container dimensions or the minimum separation distance between units in the array. The hand-calculation methods employed were Criticality Index, Surface Density and Density Analogue. These methods are described in the Nuclear Criticality Safety Guide TID-7016, Revision 2, NUREG/CR-0095.
Quality Engineering Support for Fissile Material Polishing Project
Primary Engineering Discipline: Nuclear Engineering, Quality Assurance
Client: Los Alamos National Laboratory
The fissile polishing project provided polished fissile material for fabrication into lead test fuel assemblies for use in U.S nuclear power reactors. This project was required to meet Nuclear Regulatory Commission Quality Assurance criteria from 10 CFR 50 Appendix B which were implemented in accordance with NRC Regulatory Guides and in accordance with NQA-1. LANL was required to maintain and extend its quality infrastructure in order to be in compliance with these requirements. An audit of the project resulted in a number of corrective actions that required resolution. These corrective actions included improvements in process procedures, quality assurance programs and the development and implementation of process and procedure for review evaluation and acceptance of legacy material. Legacy material consisted of polished fissile material that had been made under procedures that were not fully integrated into the approved quality program.
The schedule for implementation of the corrective actions and acceptance of the legacy material was critical since delivery of the material was required to meet the fuel fabrication schedule. The ability to meet these quality requirements was an integral part of the project’s performance goals.
TMC provided a qualified nuclear engineer with experience in quality requirements for nuclear fuel, 10 CFR 50 Appendix B, and the integration of engineering requirements. Work to be performed included revision of production procedures to accommodate quality documentation that indicated conformance with the technical requirements of the customer specification. Implementation of improvements to the quality infrastructure included the identification and implementation of Corrective Action Reports (CARs) and the identification and resolution of nonconformance reports (NCRs). In addition, the work required the development and implementation of a review and data evaluation process to demonstrate how the legacy material met the technical requirements.
During the course of this work the production procedures were revised to incorporate quality requirements, the NCR and CAR processes were improved. The backlog of NCRs and CARs were resolved and a legacy material review procedure was initiated and implemented. The result was that the material was completed and accepted by the customer within the designated schedule.
Nuclear Material Detection and Interdiction
Primary Engineering Discipline: Nuclear Engineering
Client: Los Alamos National Laboratories
TMC provided engineers with extensive experience in nuclear equipment installation at industrial sites, nuclear safety, nuclear systems analysis, risk assessments and operational logistics of nuclear systems projects to support the installation of radiation detection systems at international border crossing points. TMC’s support included:
- Delivery of nuclear detectors for deterrence of nuclear smuggling
- Selection of locations for installation of radiation detection systems
- Selection and specification for installation of radiation detection systems
- Procurement installation testing and start-up of overseas detection systems
- Establishment of a maintenance program to support foreign installed radiation detectors